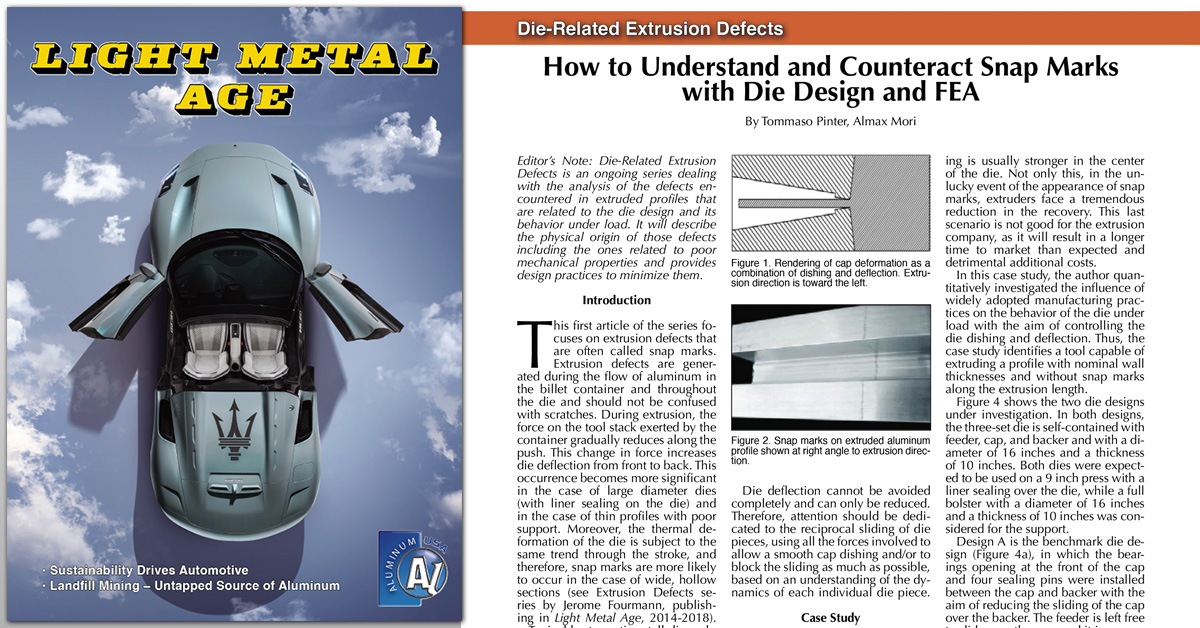
How to Understand and Counteract Snap Marks with Die Design and FEA
Abstract
Editor’s Note: Die-Related Extrusion Defects is an ongoing series dealing with the analysis of the defects encountered in extruded profiles that are related to the die design and its behavior under load. It will describe the physical origin of those defects including the ones related to poor mechanical properties and provides design practices to minimize them.
This first article of the series focuses on extrusion defects that are often called snap marks. Extrusion defects are generated during the flow of aluminum in the billet container and throughout the die and should not be confused with scratches. During extrusion, the force on the tool stack exerted by the container gradually reduces along the push. This change in force increases die deflection from front to back. This occurrence becomes more significant in the case of large diameter dies (with liner sealing on the die) and in the case of thin profiles with poor support. Moreover, the thermal deformation of the die is subject to the same trend through the stroke, and therefore, snap marks are more likely to occur in the case of wide, hollow sections (see Extrusion Defects series by Jerome Fourmann, publishing in Light Metal Age, 2014-2018).